
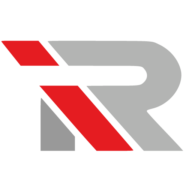
6 Strategies to Lower Manufacturing Costs
Many manufacturers of wooden products face rising operating costs, impacting your bottom line and competitiveness. If production expenses continue to increase, you may need to raise prices or compromise quality, risking customer loss and brand damage.
We understand the frustration of balancing efficiency and quality. It is crucial to find effective solutions to lower costs. By exploring innovative technologies like laser cutting, you can enhance processes and improve product offerings.
Escalating operating costs can disrupt operations and hinder financial objectives. For example, if production expenses surge unexpectedly, you may have to choose between raising prices or compromising quality, which can alienate loyal customers and damage your brand’s reputation.
Tackling this issue is imperative. If left unchecked, rising costs can lead to financial strain, affecting your business and personal aspirations. You may miss opportunities for growth or innovation, which can be detrimental in a competitive landscape.
We understand the challenges faced by professionals in the woodworking industry. Our insights into this sector allow us to empathize with your circumstances. It is vital to confront these escalating costs directly to maintain competitive advantage and ensure your business’s sustainability.
Effective solutions can help you navigate these challenges. By implementing advanced technologies, you can alleviate some burdens of rising costs. The following strategies will guide you toward impactful resolutions.
Envision a future where your production processes are more efficient, allowing you to maintain quality while reducing expenses. Progress is attainable as you explore these innovative solutions.
For instance, consider the advantages of CNC Laser cutting machines. These tools can enhance precision and efficiency in your operations, potentially leading to significant cost savings. Let us explore these strategies and empower your business for a brighter future.
Let us guide you through steps that can transform your operations. These strategies serve as a roadmap to address rising costs. By implementing these techniques, you can improve efficiency and maintain quality in your production processes.
As you read on, you will discover insights that can empower your woodworking business. Each strategy equips you with tools to navigate industry complexities. Together, we can work towards a more sustainable and profitable future.
Prepare to explore effective solutions and take the first step toward optimizing your operations.
1.Automate Your Production Process
In today’s competitive environment, manufacturers face pressure to reduce expenses while maintaining quality. Research shows that automating your production process can lead to savings of around 30 percent. Failing to adapt may result in lost contracts and diminishing profits.
Are you a manufacturer striving to meet demand while managing rising operational costs? Without automation, you risk falling behind competitors.
The good news is there are effective strategies to enhance your operations. In the following sections, we will explore actionable solutions that can transform your production process and positively impact your bottom line.
Many manufacturers of wooden products face inefficiencies in their production processes. For example, a small furniture workshop may struggle to keep up with orders due to outdated machinery and manual methods. This not only delays deliveries but also frustrates skilled artisans who take pride in their craftsmanship.
When production slows, it can lead to missed opportunities and lost contracts, ultimately affecting the bottom line. As a manufacturer dedicated to premium furniture, you understand the importance of meeting customer expectations while optimizing material efficiency.
Allowing this issue to persist risks your competitive advantage in a market that demands both quality and speed. By addressing these inefficiencies through automation, you can alleviate daily frustrations and focus on crafting exceptional products that resonate with your customers.
To address inefficiencies in your production process, consider implementing the following solutions:
– Invest in CNC laser technology: This technology enhances precision and speed. For example, a workshop adopting CNC laser cutting may reduce waste and improve design accuracy. Evaluate your machinery and identify areas for enhancement.
– Integrate workflow automation software: This software streamlines order management and inventory tracking. Automating order processing leads to quicker turnaround times. Provide necessary training for your team to maximize the software’s potential.
– Upgrade to modern machinery: Replacing outdated equipment with contemporary alternatives improves efficiency. For instance, investing in automated saws may increase production speed. Research options and budget for enhancements.
– Implement lean manufacturing principles: This approach minimizes waste while maximizing productivity. Conduct a value stream mapping exercise to identify inefficiencies. Engage your team for effective execution.
– Train your workforce: Regular training enhances skills and efficiency. Workshops on new technologies empower your team to utilize tools effectively. Allocate time and resources for ongoing education.
By applying these solutions, you can address challenges in your production process. Each strategy improves efficiency and positions your business for sustained growth in a competitive market. For more information on CNC laser fibre technology, visit this link.
Begin by evaluating your current production process. Identify one area where automation could significantly impact, such as incorporating CNC laser technology to enhance cutting.
Set a realistic goal, like reducing waste by ten percent in the next month. Monitor progress and adjust as needed to see timely results and motivate your team.
As you gain confidence, explore more areas for automation or machinery enhancements. Each step builds on the last, allowing you to scale improvements based on your needs.
For tailored solutions, contact us. We are here to help you maximize production efficiency and maintain your competitive edge in manufacturing.
2.Optimize Material Usage
Imagine your production line halted due to wasted materials. Inefficient material usage can increase costs by up to 30 percent. Every scrap of wood not utilized effectively represents lost revenue.
Are you seeking ways to enhance material usage? Overlooking this issue could lead to financial strain and hinder your competitiveness in the woodworking sector.
Practical solutions are on the way. In the following sections, we will explore strategies to maximize material efficiency and improve your bottom line.
The central issue is inefficient material use, which increases production costs. A wooden products manufacturer found that about 20 percent of their raw materials were wasted due to improper cutting techniques. This affected profit margins and delayed project timelines, frustrating both the team and clients.
As a manufacturer committed to high-quality craftsmanship, you know every piece of wood holds value. Allowing this issue to persist could lead to higher expenses and lost opportunities in a competitive market.
Every day, you face the challenge of balancing quality with efficiency. By addressing material usage, you can optimize processes and improve overall productivity.
To address material inefficiency, consider implementing these strategies:
- Invest in advanced cutting technology: Upgrading to precision cutting tools can reduce waste. For example, a woodworking manufacturer that transitioned to laser cutting observed a 25 percent reduction in material waste within the first month.Conduct regular training sessions: Educating your team on best practices in material handling can improve usage. A woodworking company that held monthly workshops noted a 15 percent increase in material efficiency.Implement a material tracking system: Utilizing software to monitor material usage can help identify waste patterns. One woodworking manufacturer found that tracking materials resulted in a 20 percent decrease in costs over six months.Optimize design processes: Reviewing and refining product designs can minimize waste. A simple redesign of a popular product enabled one woodworking company to save 30 percent in raw material costs.
These solutions can be applied promptly with the right resources. For instance, investing in advanced cutting technology may require initial capital but can yield substantial long-term savings. By addressing material usage now, you can enhance productivity and maintain a competitive edge in the woodworking market.
To implement these strategies, start by selecting one area to focus on. For example, if you invest in advanced cutting technology, research the latest laser cutting solutions. Schedule a demonstration to see how it integrates into your production line.
Next, measure your current material waste over a week to establish a baseline for comparison once you implement new tools or techniques.
As you observe improvements, consider scaling these changes across your operations. Introduce regular training sessions for your team to ensure alignment with best practices.
For tailored advice, visit our website for resources on maximizing material efficiency. Together, we can enhance your productivity and maintain a competitive edge in manufacturing.
3.Boost Production Efficiency
In today’s competitive landscape, manufacturers must optimize operations. Research shows that those who do not enhance production efficiency may lose up to 20 percent of potential output. Consider the impact on your bottom line if you rely on outdated processes.
Are you struggling to meet demand while maintaining quality? Each day without a solution could mean missed opportunities and rising costs.
The good news is that proven strategies exist to address these challenges. In the following sections, we will explore how laser technology can transform your production processes and help you achieve your goals.
The central challenge is sustaining production efficiency while meeting increasing demand. For example, a manufacturer of wooden products recently received a significant order for custom furniture. Despite their craftsmanship, outdated machinery limited their production capabilities, leading to missed deadlines and dissatisfied clients. This scenario is common in the woodworking industry.
Allowing this issue to persist can result in lost revenue and a tarnished reputation. Each day spent on inefficient processes affects output and consumes valuable time and resources. By addressing these challenges with laser technology, manufacturers can enhance operations, improve precision, and restore their competitive edge.
To enhance production efficiency, consider implementing these solutions:
- Invest in laser cutting technology: This technology enables faster, more precise cuts, minimizing waste and improving turnaround times. For example, a woodworking manufacturer may transition from traditional saws to laser cutters, potentially increasing production speed by 30 percent.Automate routine tasks: Automation streamlines repetitive processes, allowing skilled labor to focus on complex tasks. A woodworking manufacturer could introduce automated sanding machines to enhance consistency and reduce labor costs.Optimize workflow layout: An efficient layout reduces movement and maximizes productivity. Rearranging workstations based on production flow may eliminate unnecessary steps and improve overall efficiency.Utilize data analytics: Data analytics helps identify production bottlenecks. Tracking machine performance may indicate when maintenance is needed, preventing costly downtime.Train employees on new technologies: Continuous training ensures your team is proficient in the latest technologies. A woodworking manufacturer can schedule regular workshops to keep staff informed on best practices and new tools.
Implementing these solutions requires an initial investment in technology and training. However, the long-term benefits may include enhanced efficiency, reduced costs, and a stronger competitive position in the woodworking market.
To enhance production efficiency, evaluate your current processes and identify where to integrate laser cutting technology. Conduct a trial run with a laser cutter on a small batch to assess speed and precision improvements.
Next, review your workflow layout. Gather your team for a brainstorming session on potential adjustments to enhance productivity. Implement one change and monitor the results over a week.
Utilize data analytics tools to track production metrics. Set up a simple dashboard to visualize performance and identify bottlenecks, enabling informed decisions based on real-time data.
As you adapt these solutions, remember that scaling is essential. Start small, then gradually expand changes across operations to minimize disruption while maximizing benefits.
We encourage you to reach out for insights on how laser technology can transform your production processes. Together, we can help you achieve your objectives and maintain a competitive edge in manufacturing.
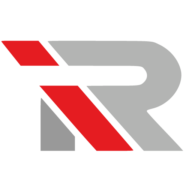
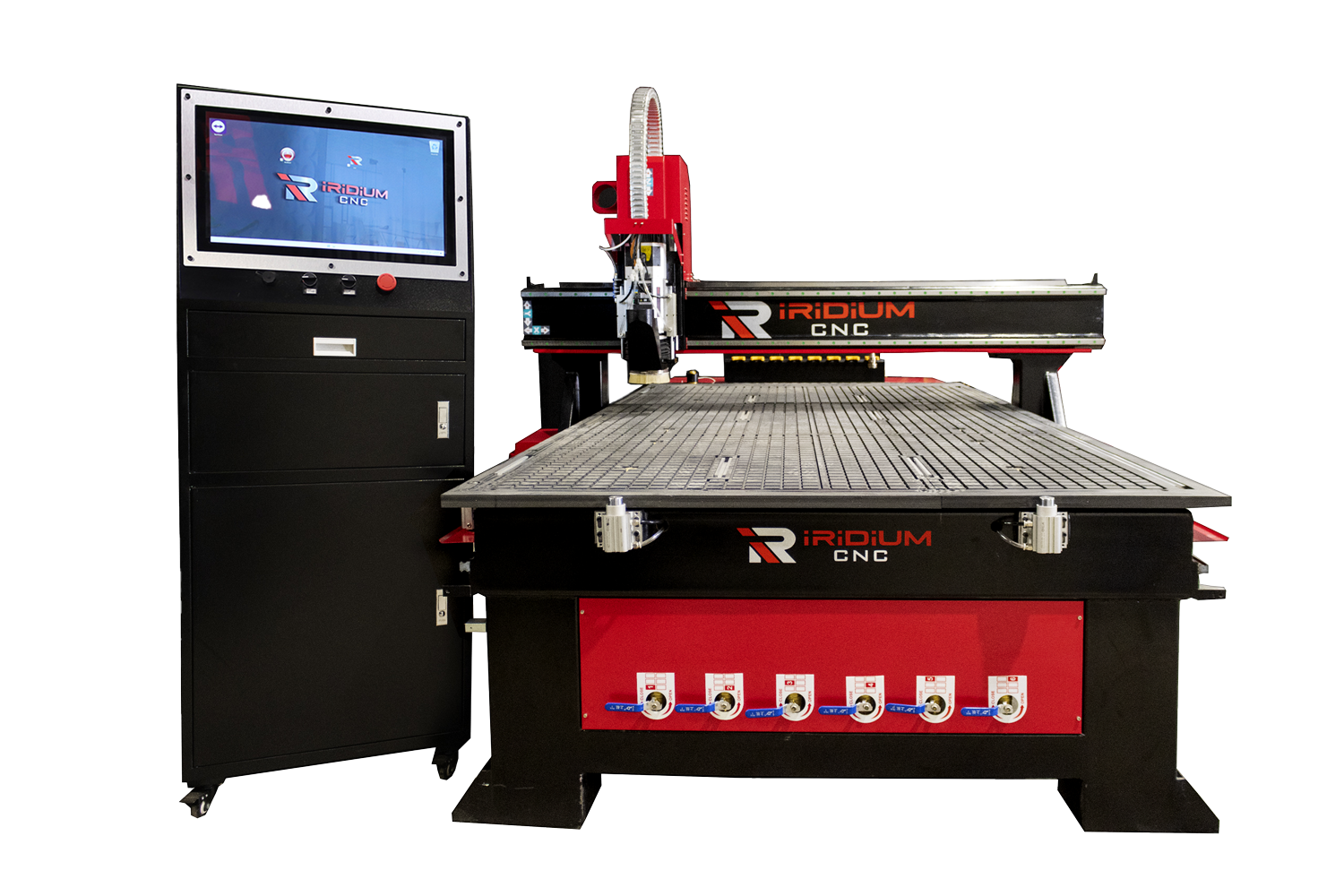
CNC Router
CNC routers are versatile machines used for cutting and shaping various materials.
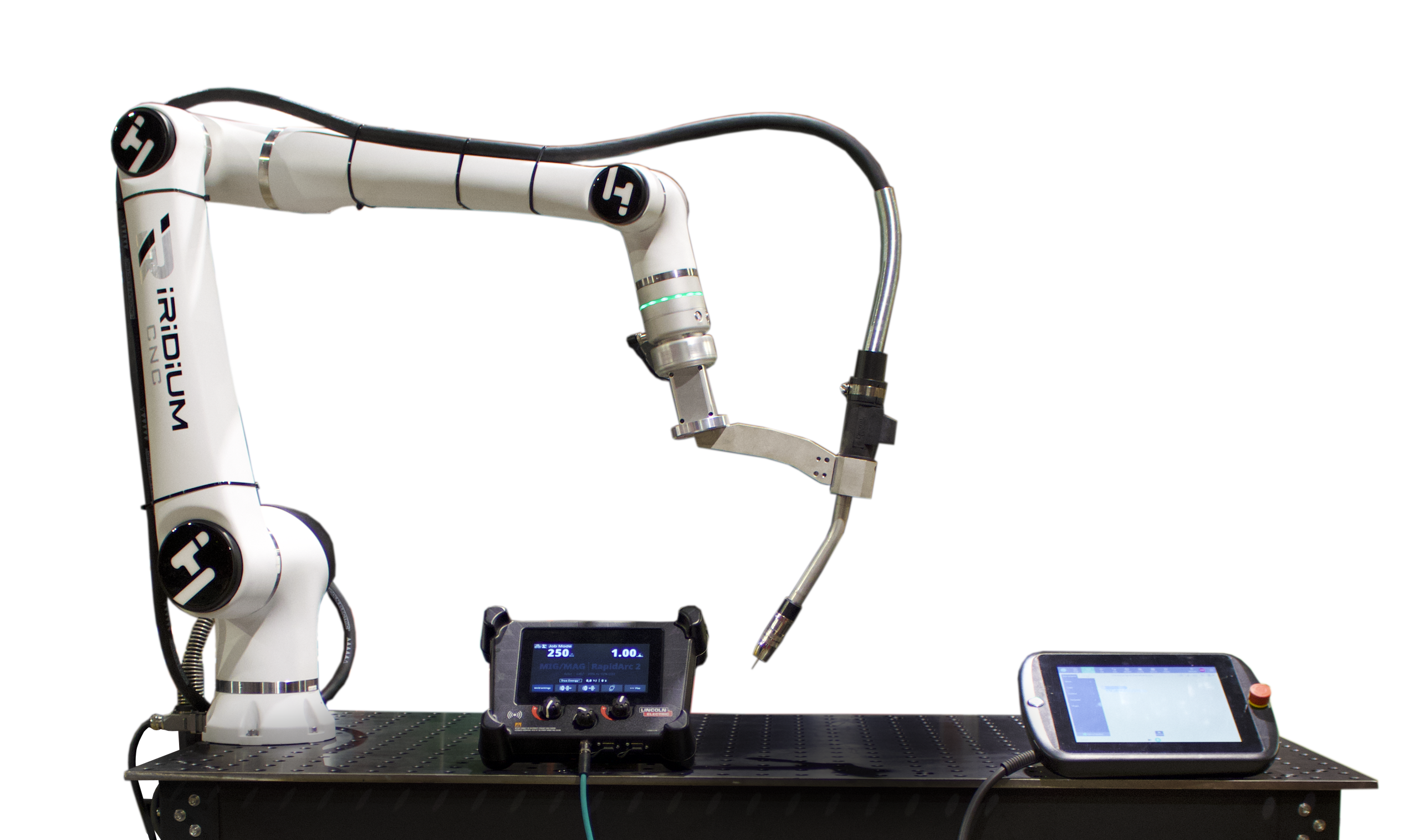
Robotic systems
Robotic systems enhance automation and efficiency in manufacturing processes.
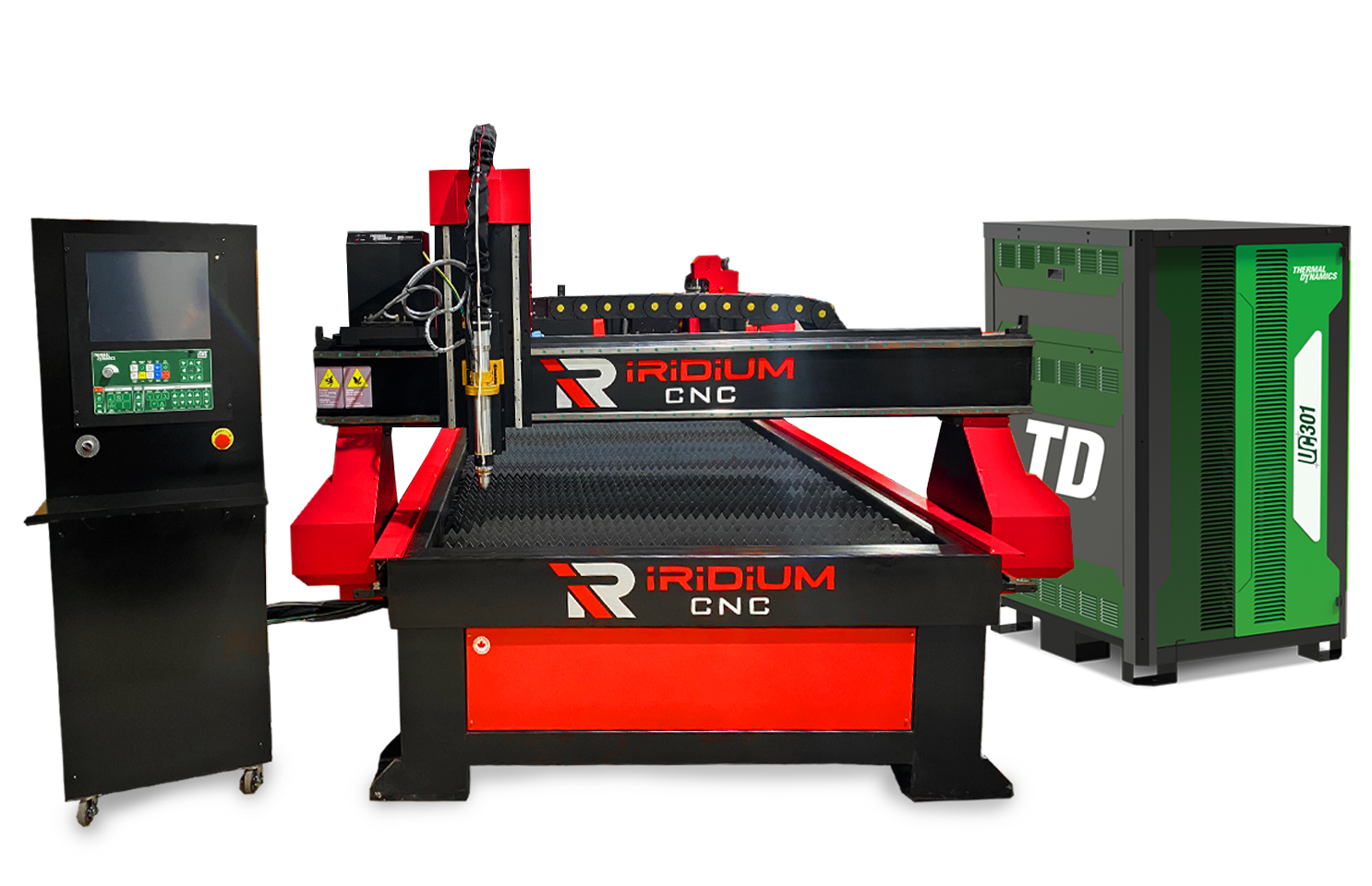
CNC Plasma cutting machine
CNC plasma cutting machines are essential for precise metal cutting in various industries.
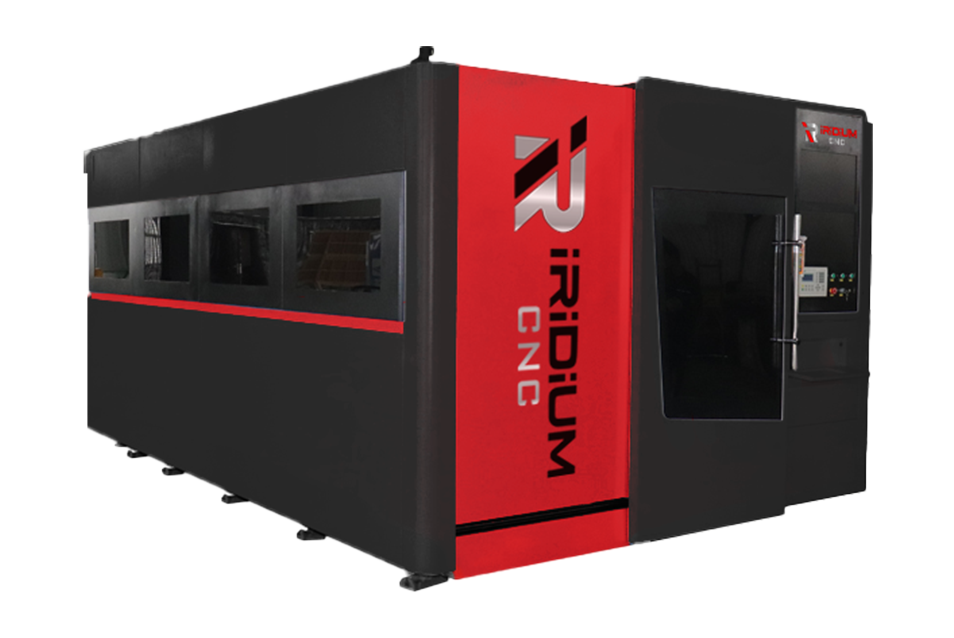
CNC Laser cutting machine
CNC laser cutting machines provide high precision and speed for various cutting applications.
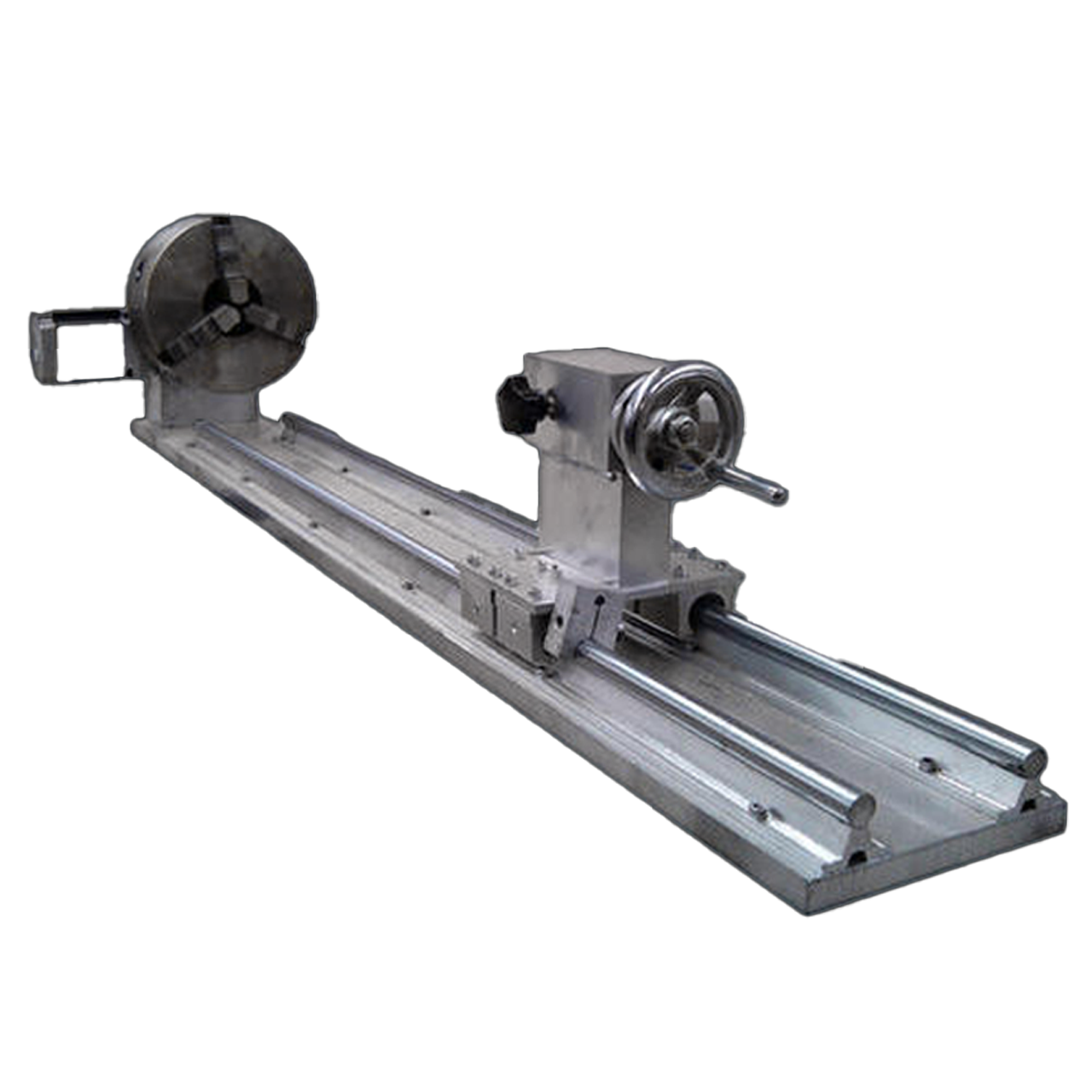
Axe rotatif
Axes rotatif are essential components for expanding the functionality of CNC routers.
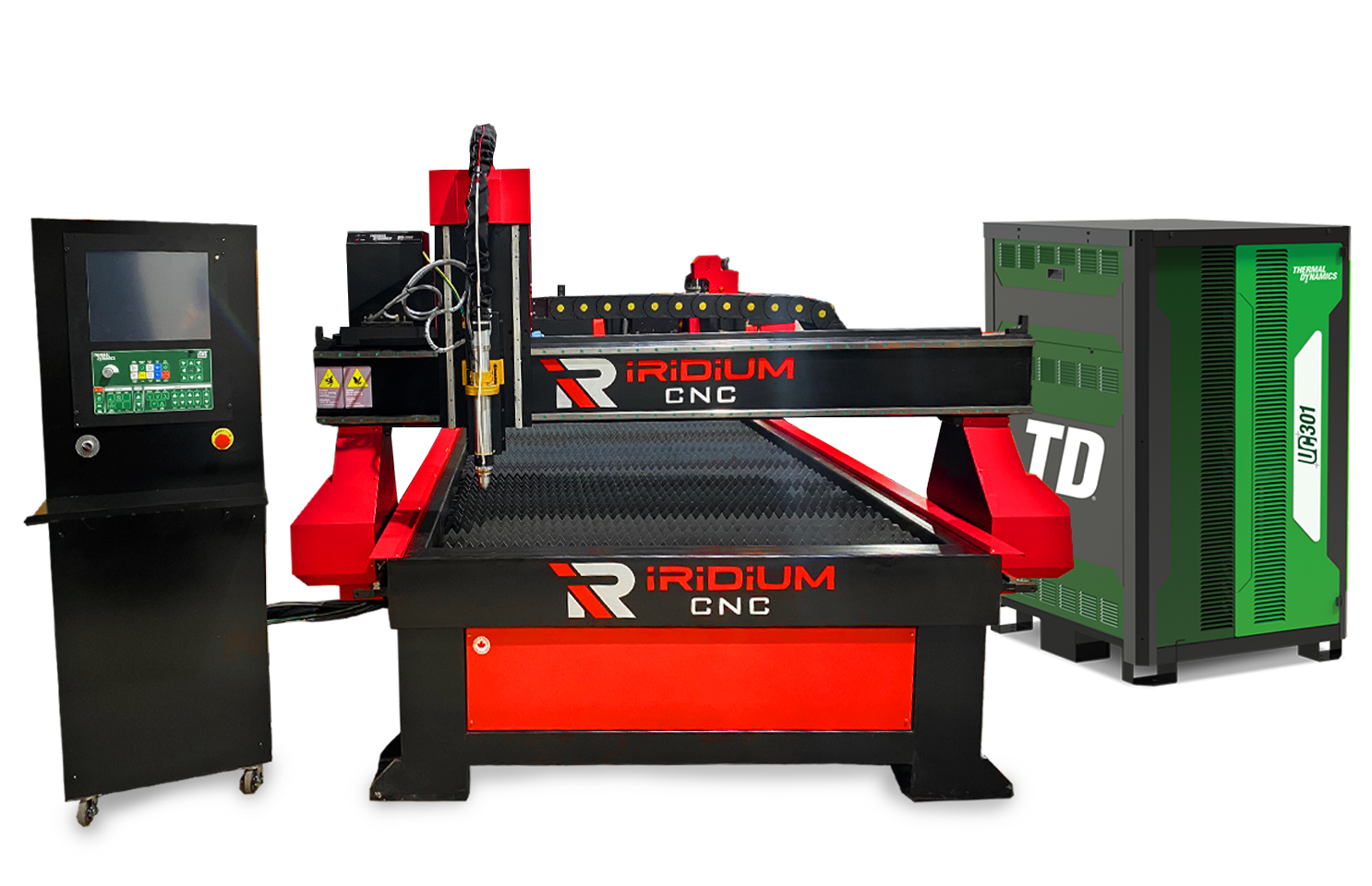
CNC Plasma HD
CNC Plasma HD delivers high-definition cutting with impressive accuracy and speed.
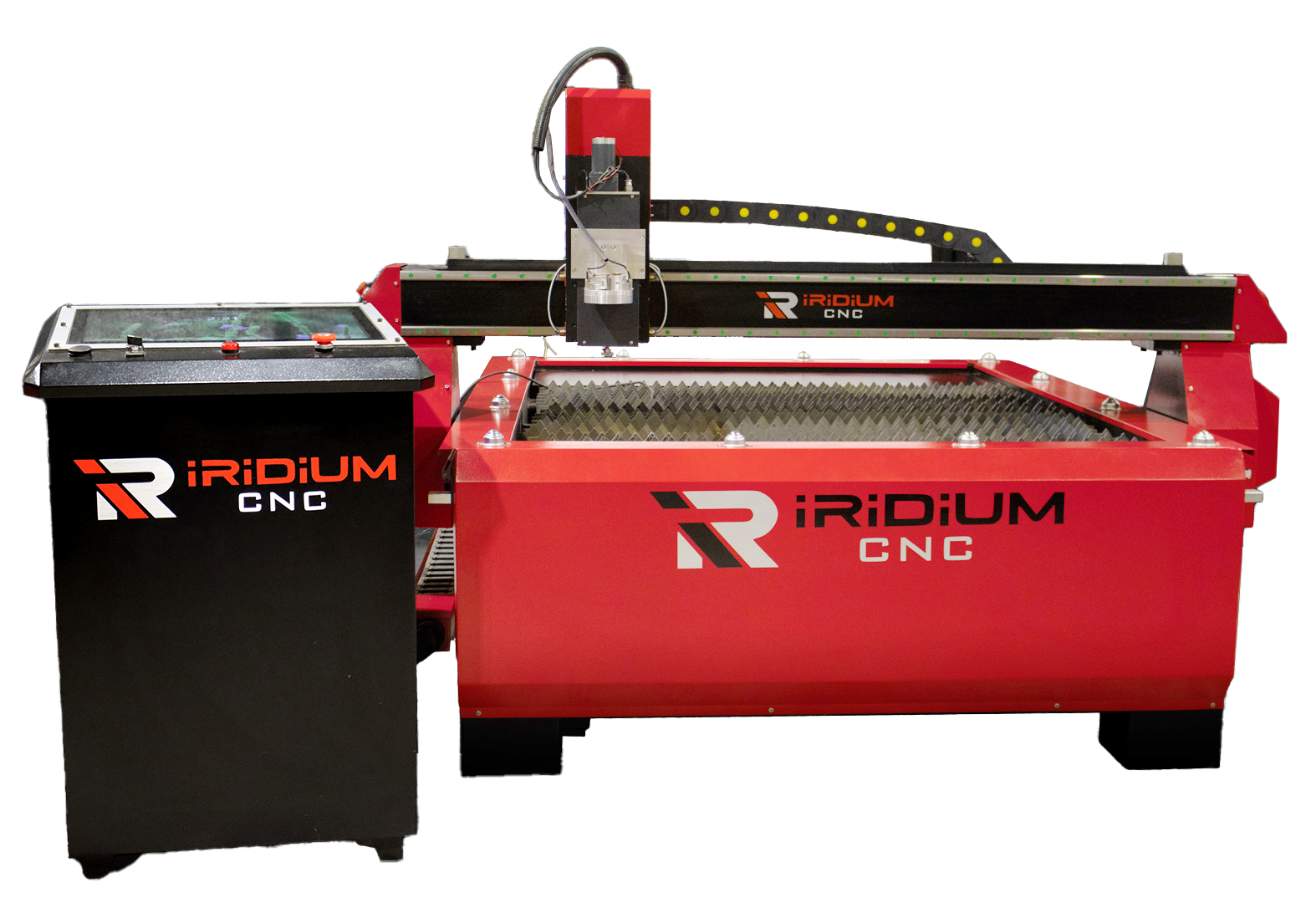
CNC Plasma Coupe tuyaux
Designed for cutting metal pipes, CNC Plasma Coupe combines precision with efficiency.
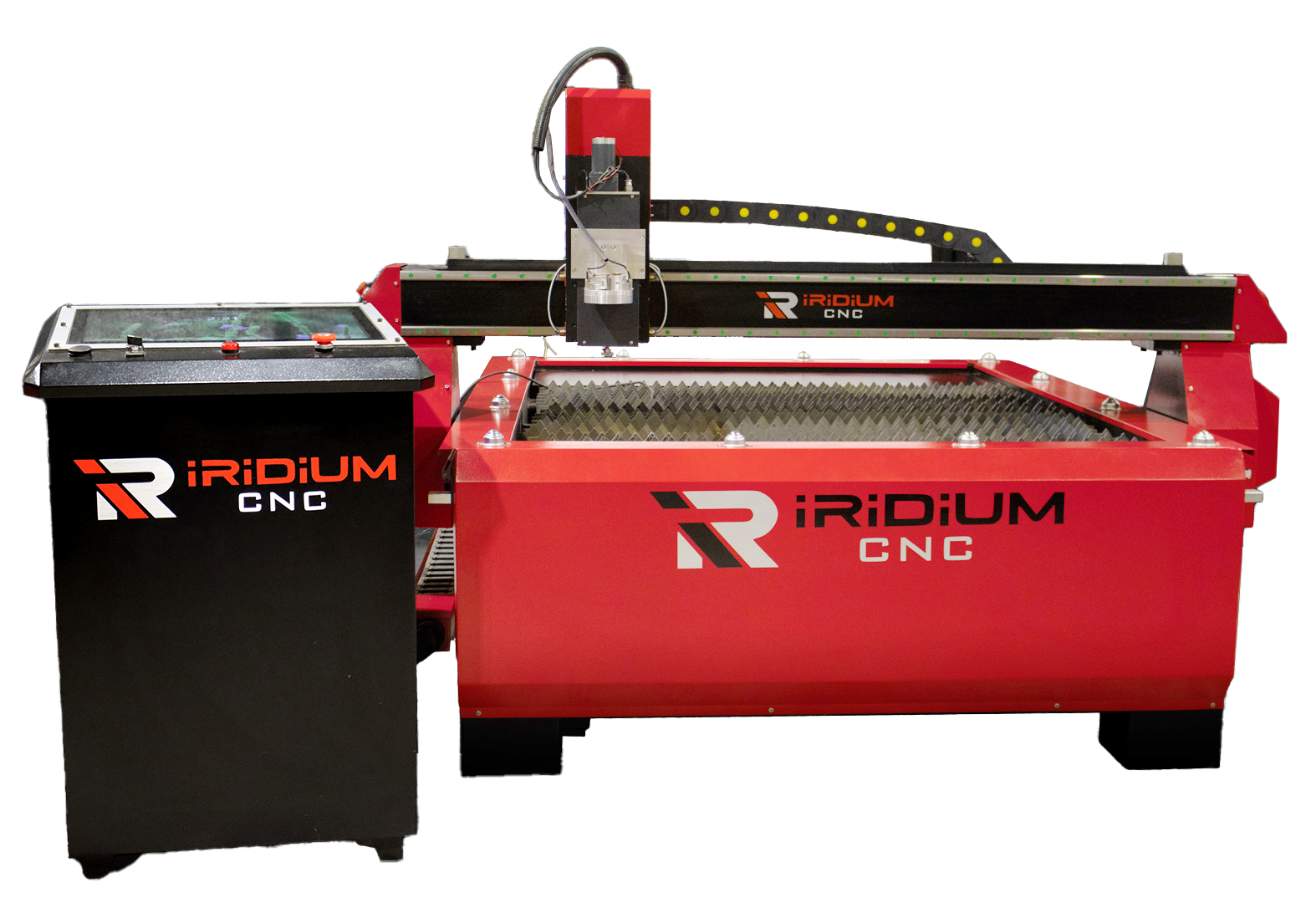
CNC Plasma Pro
CNC Plasma Pro uses high-precision plasma technology for efficient metal cutting.
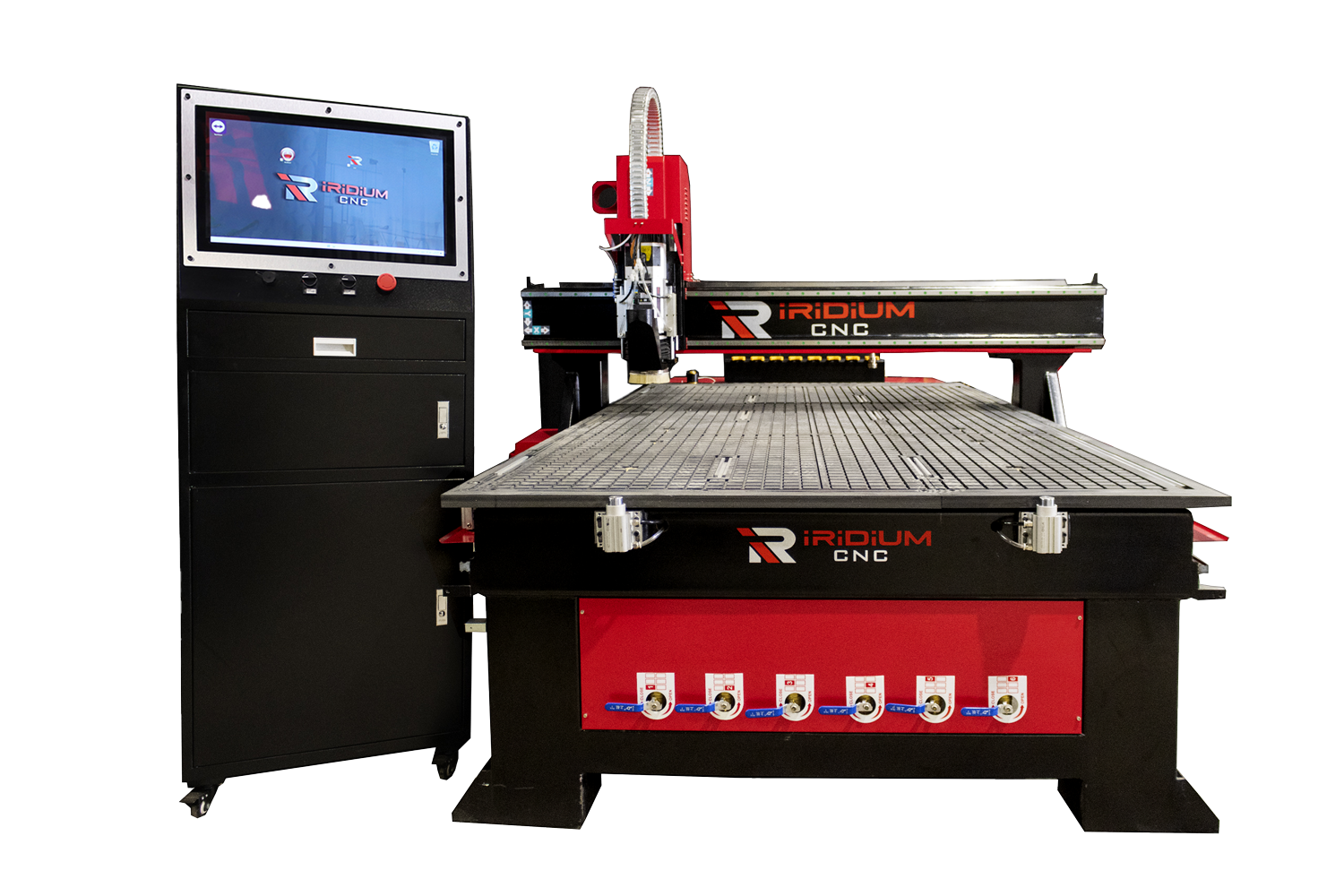
Routeur CNC – Série Pro Max
The Serie Pro Max Router provides enhanced features for advanced machining requirements and versatility.
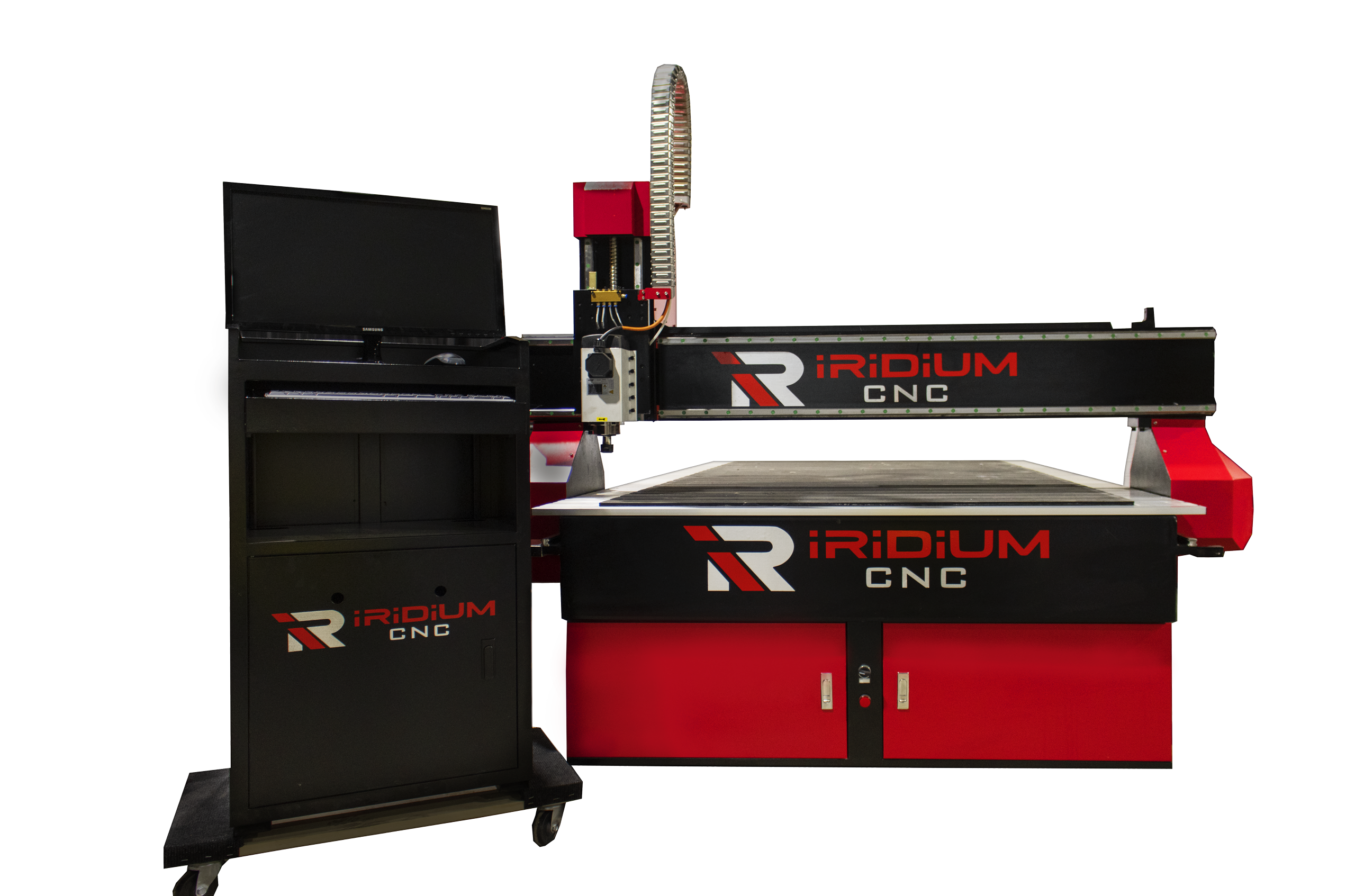
Routeur CNC – Série Pro
The Série Pro CNC Router offers high-performance cutting capabilities suitable for a wide range of materials.
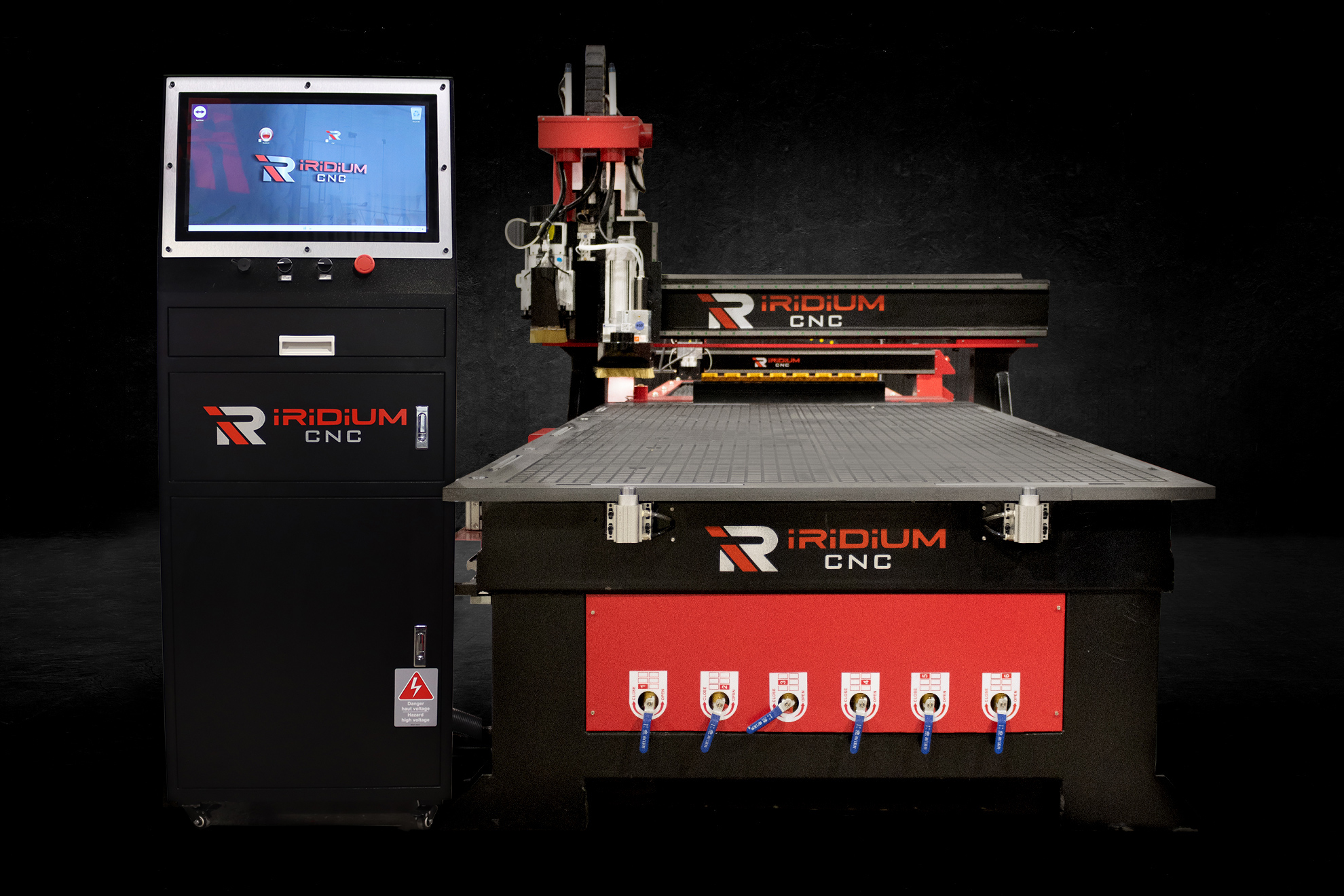
CNC Série PRO Multi Drill
High performance CNC machine designed for multi-drilling operations, optimized for precision and efficiency.
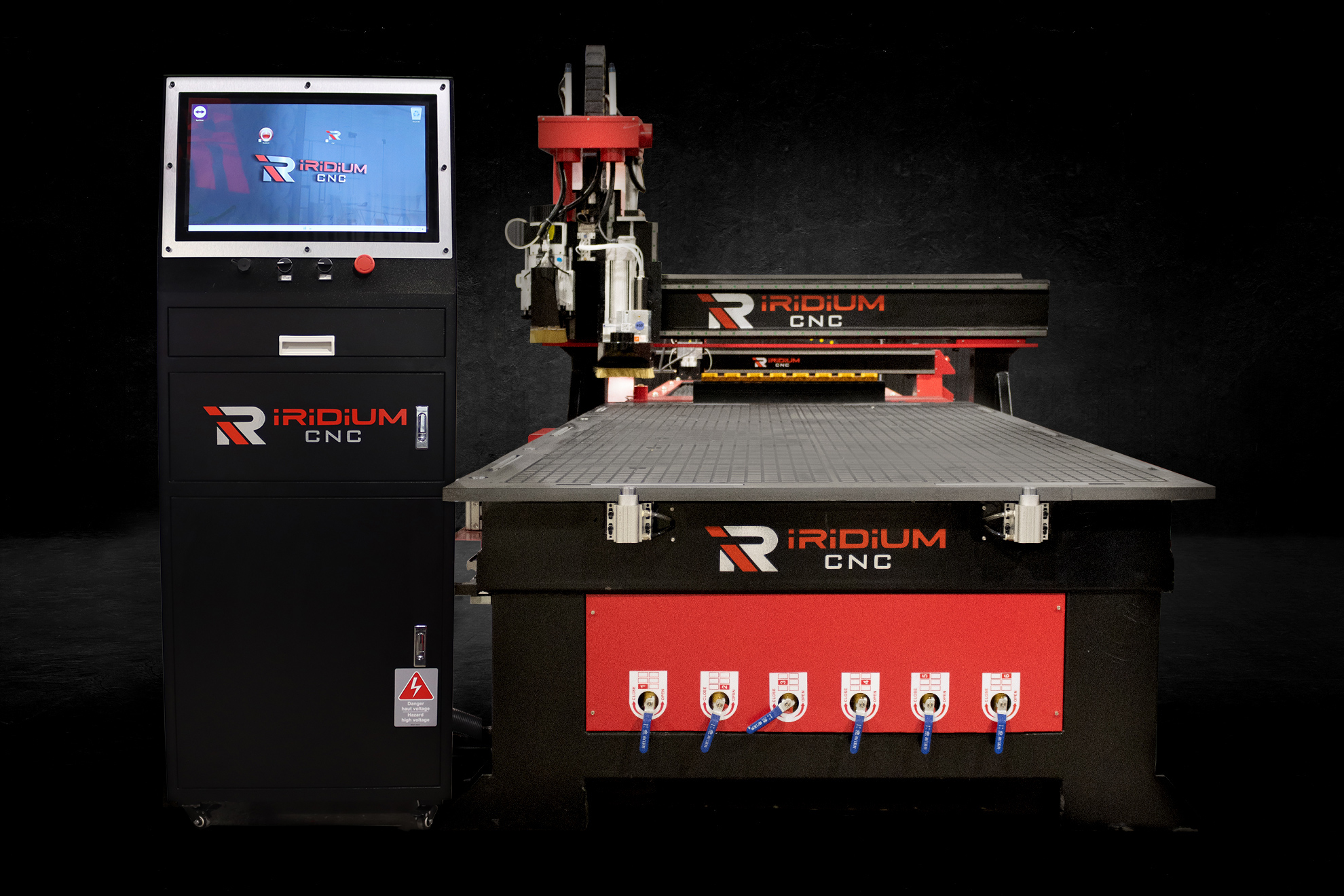
Routeur CNC – Série Pro Max MD
Série Pro Max MD Router is designed for multi-drilling and precise cutting tasks with excellent performance.
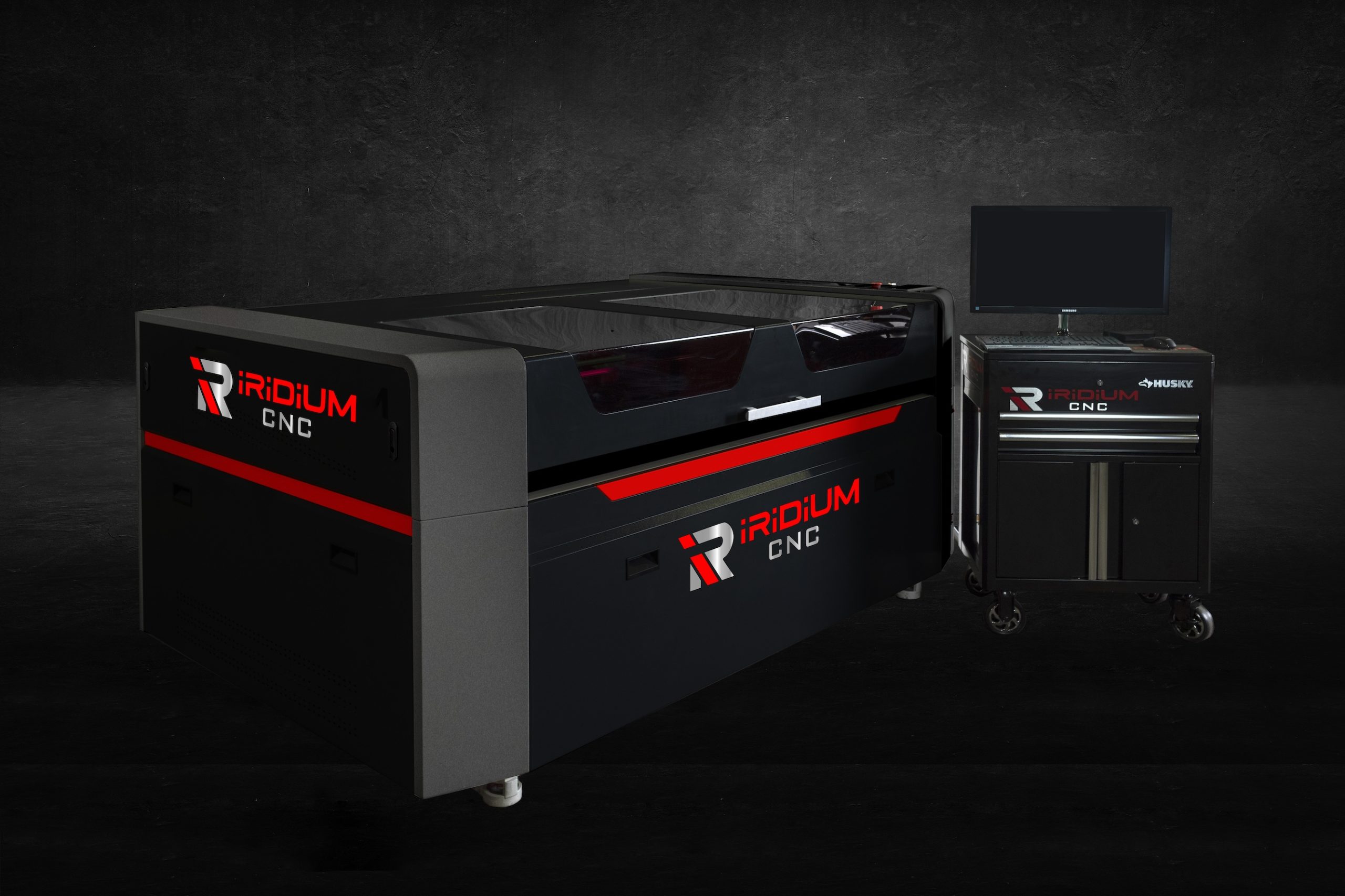
Laser CO2
Laser CO2 technology is known for its precision and versatility in cutting and engraving materials.
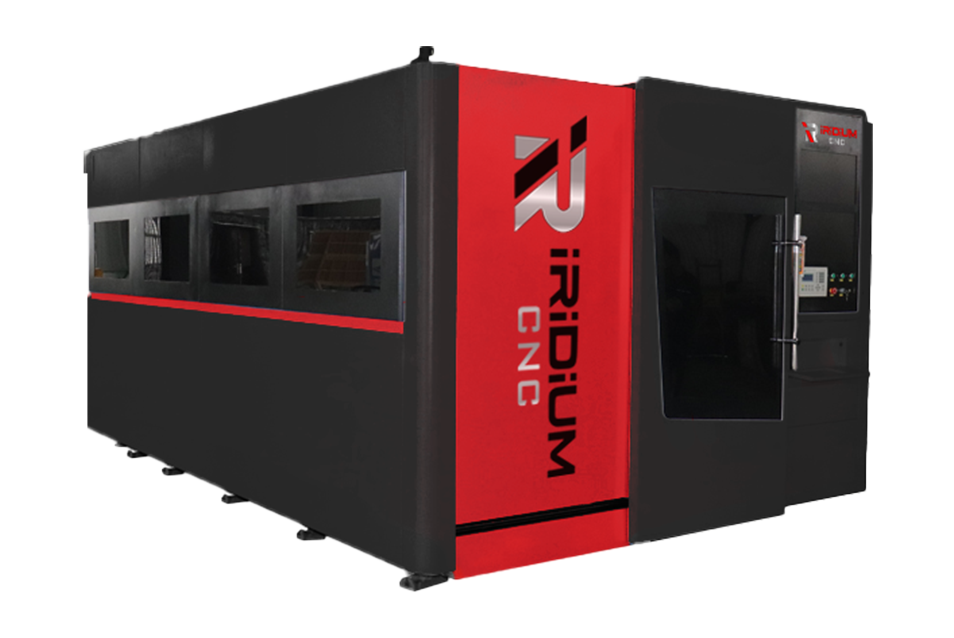
Laser Fibre
High precision fibre laser cutting system engineered for industrial applications.
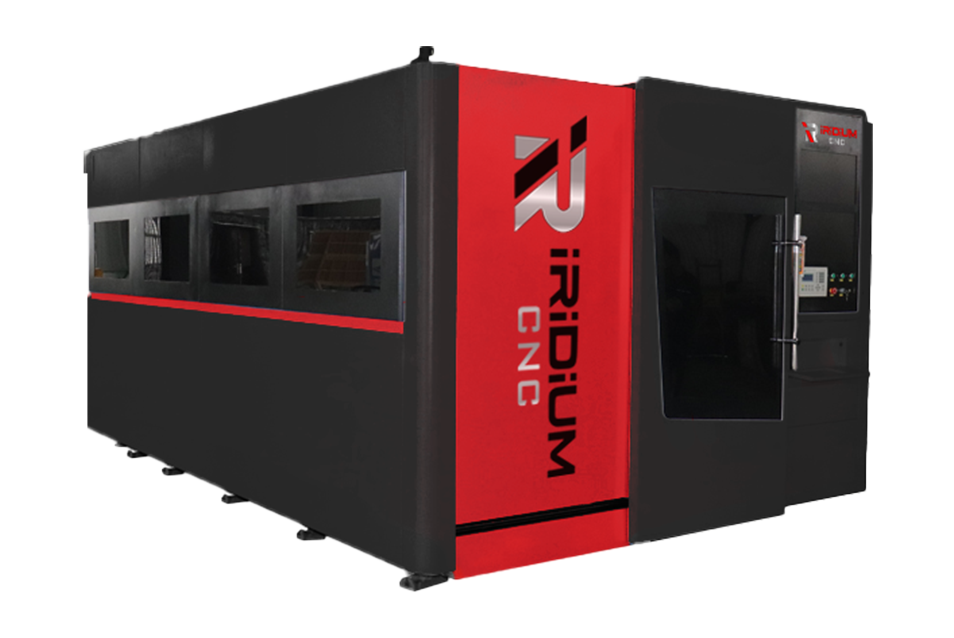
CNC Laser fibre
CNC Fibre Laser provides exceptional cutting quality while maintaining faster production speeds.
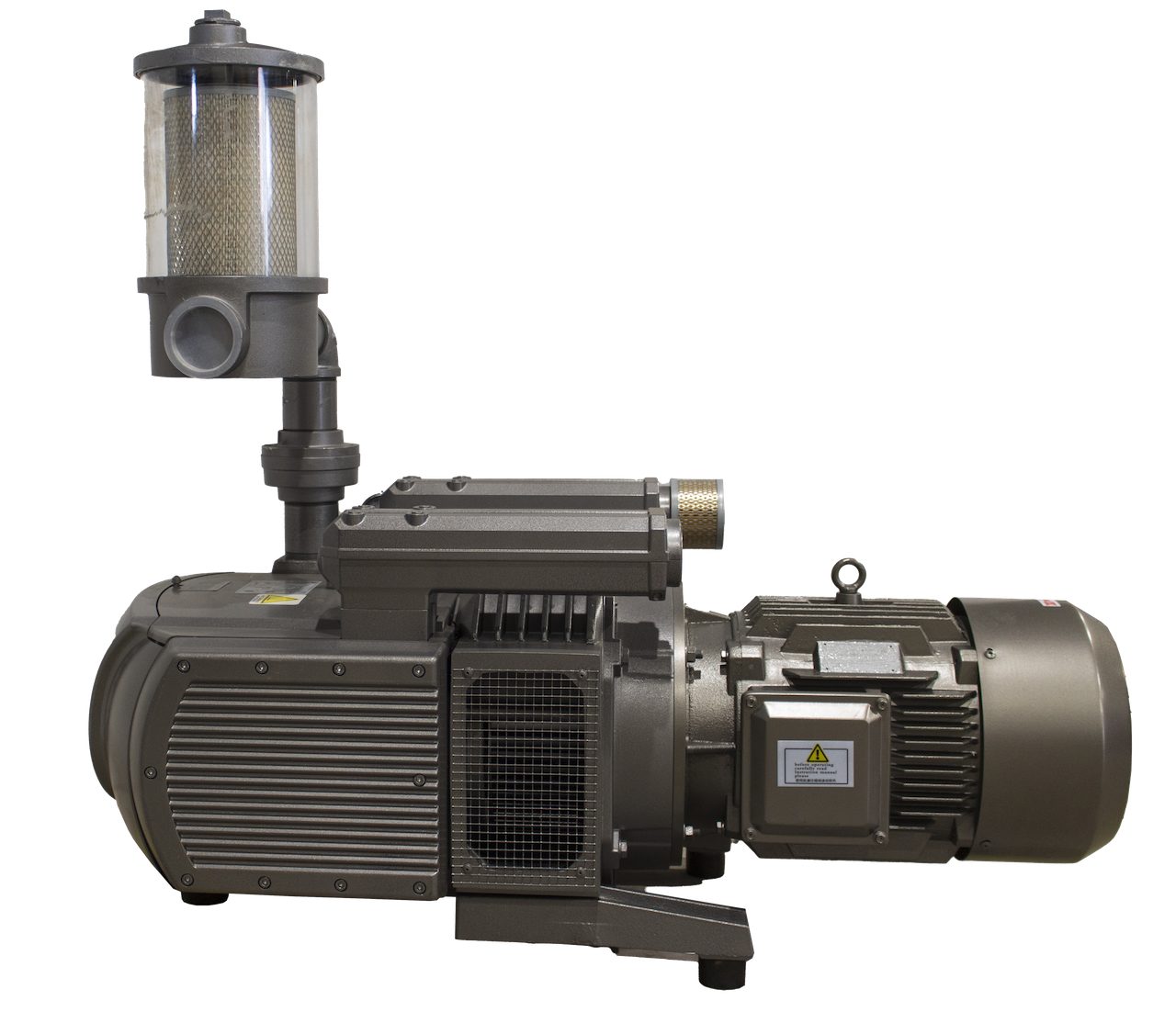
Pompe aspirante
Pompe aspirante provides reliable suction for holding materials securely during machining processes.
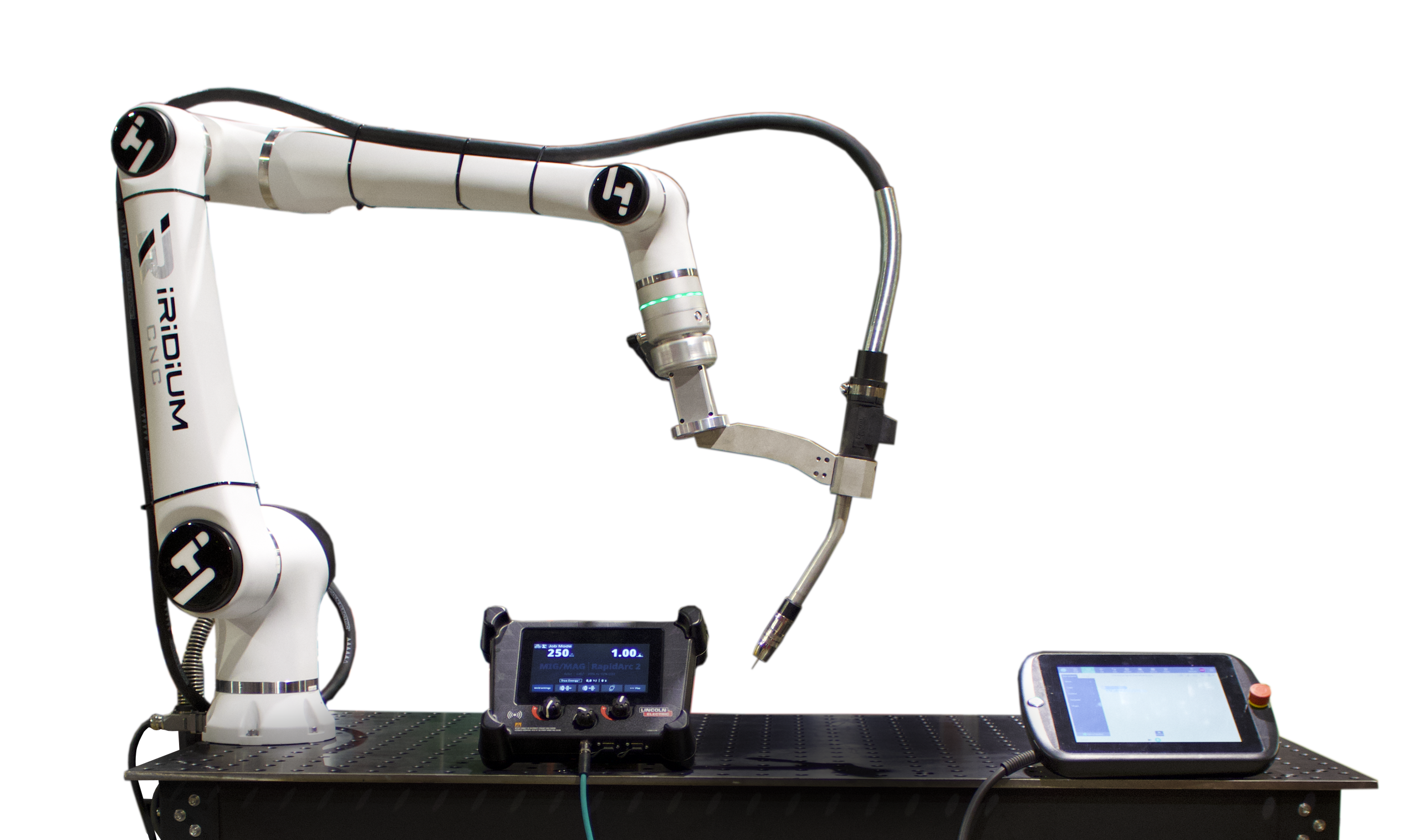
Robot Collaboratif
Collaborative robot designed for flexible automation in modern manufacturing environments.
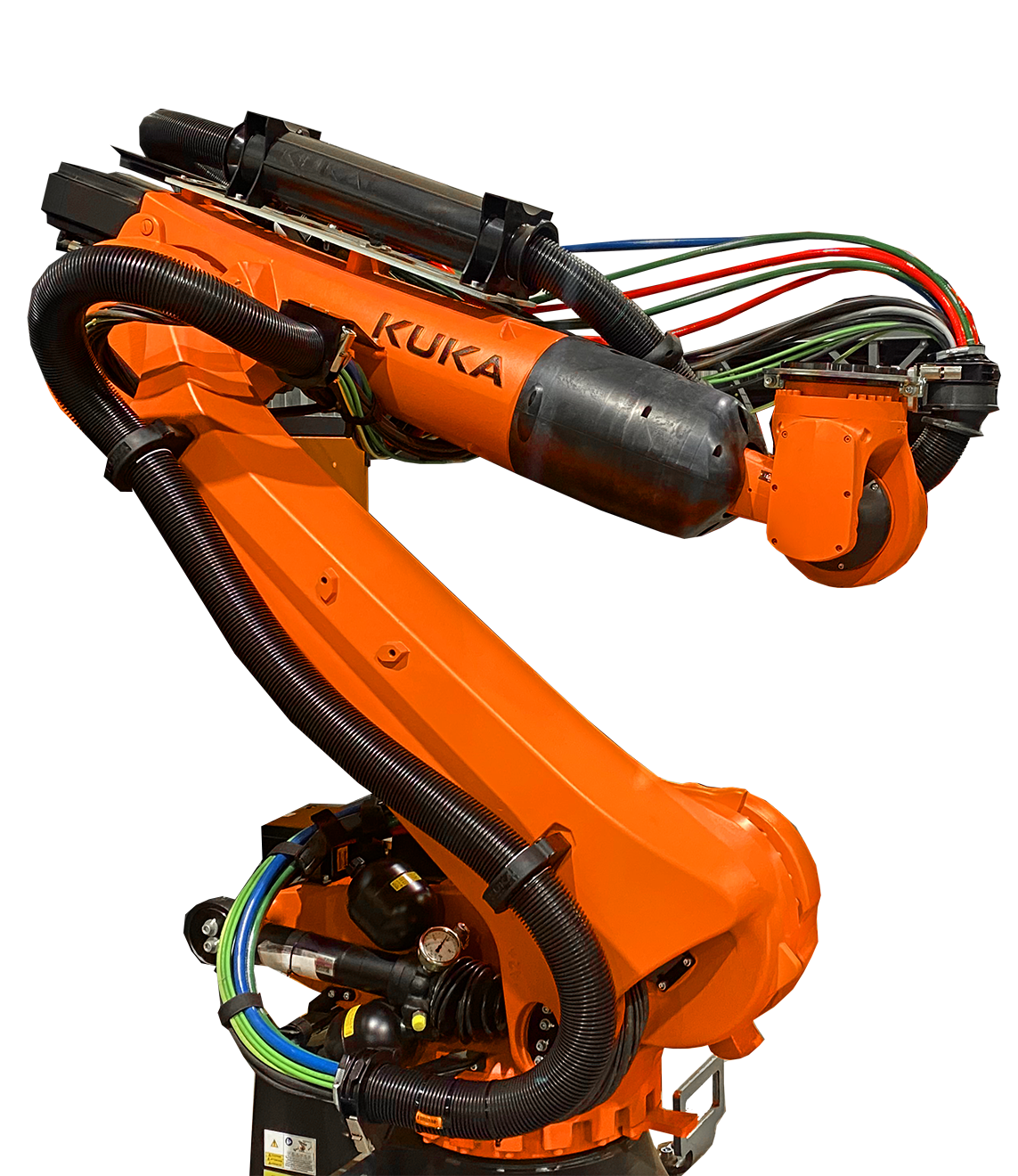
Robot coupeur
Robot coupeur specializes in automated cutting processes, enhancing productivity in manufacturing environments.
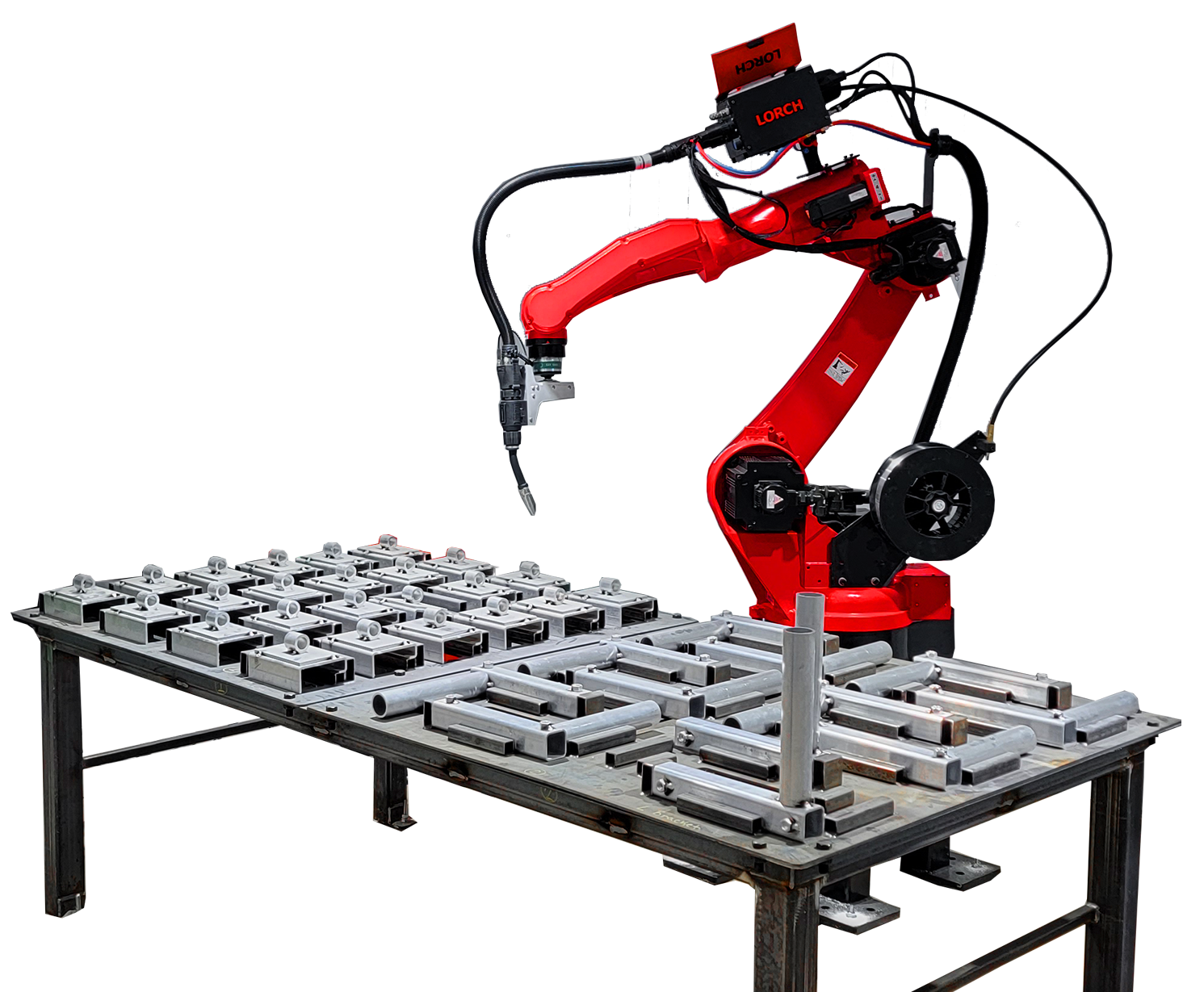
Robot soudeur
Robot soudeur automates welding tasks, providing greater flexibility and accuracy in production.
4.Achieve Consistent Quality
In woodworking, achieving consistent quality is essential. Research shows that nearly 30% of manufacturers face quality challenges that can lead to financial losses. Consider the impact on your business if these obstacles persist.
Are you struggling to meet the high standards your clients expect? Inconsistent quality can harm your reputation and result in lost sales. If unaddressed, these issues can lead to wasted materials, increased labor costs, and a decline in customer satisfaction.
However, effective solutions are within reach. In the following sections, we will explore strategies to enhance quality and optimize your production processes. Get ready to transform your operations and secure your competitive advantage.
The central challenge is maintaining consistent quality in your woodworking products. This can lead to costly errors and dissatisfied customers. For example, a furniture manufacturer may receive feedback about uneven finishes, affecting their reputation and resulting in expensive returns.
As a producer of wooden products, you know your clients expect high standards. If quality issues persist, you risk damaging your brand and losing business. The pressure of reworking products or addressing complaints can be overwhelming.
By tackling these quality challenges, you can enhance production processes and boost customer satisfaction. The solutions we will discuss will help you navigate these obstacles and achieve the excellence your brand is known for.
To maintain consistent quality, consider these effective solutions:
- Implement laser technology: CNC Laser Fibre technology enhances accuracy in woodworking processes, minimizing human error and promoting uniform finishes. For instance, a woodworking business can achieve precise cuts and engravings, improving customer satisfaction.Standardize quality control processes: A robust quality control system helps identify issues early. Regular inspections and standardized checklists ensure every product meets high standards. For example, a woodworking manufacturer could implement weekly reviews of finished products to catch inconsistencies before they reach customers.Invest in employee training: Ongoing training enhances your team’s skills and awareness of quality standards. A well-trained workforce is more likely to produce consistent results. Consider scheduling monthly workshops on best practices in woodworking.Utilize feedback loops: Actively seek customer feedback to refine your processes. This helps you understand expectations and adjust production accordingly. For instance, a woodworking manufacturer could create a simple survey for customers to share their experiences with product quality.Adopt advanced software solutions: Software that tracks production metrics helps identify trends and areas for improvement. This data-driven approach allows for informed decision-making. A woodworking manufacturer could use software to analyze defect rates and adjust processes to reduce them.
By integrating these solutions into your operations, you can enhance quality, reduce costs, and boost customer satisfaction. Each step towards consistency solidifies your reputation in the woodworking industry.
To implement these solutions, start by selecting one area to focus on. If you choose to adopt laser technology, arrange a demonstration with a local supplier to observe its benefits firsthand.
Next, conduct a quality audit of your existing processes. Identify one product line with frequent quality issues. Document the challenges and gather insights from your team to establish a clear baseline for measuring improvements.
As you see results, consider scaling these solutions across your operation. For example, if employee training proves beneficial, extend it to all staff members to ensure a consistent approach to quality.
Finally, reach out for more information on how Iridium CNC can assist your journey toward improved quality. Our team is ready to support you in implementing these strategies and achieving your business goals.
5.Innovate to Compete
In today’s competitive environment, many wooden product manufacturers face a significant challenge. Research shows that many companies struggle to manage operating costs. This highlights the need for effective solutions.
Are you feeling pressure to innovate while controlling costs? Not adapting can lead to setbacks. If your production processes do not evolve, you risk losing your competitive edge and market share.
However, practical solutions are on the way. We will explore innovative strategies to streamline operations and reduce costs effectively.
The central challenge is innovating while managing operating costs. For example, a furniture manufacturer reliant on traditional methods may struggle to compete with rivals using advanced laser technology. This impacts their output and ability to create intricate designs that engage customers.
As a result, they risk losing market share and customer loyalty. Watching competitors thrive while they remain unchanged can be overwhelming. If unaddressed, this could lead to decreased profitability and potential business closure. Embracing innovation is not just a choice; it is a necessity for survival in today’s marketplace.
To innovate while managing operating expenses, consider these strategies:
- Adopt laser technology: Implementing laser cutting enhances accuracy and minimizes waste. For instance, a furniture manufacturer may transition to laser technology to create intricate designs that attract customers while reducing material costs, potentially leading to a 30% decrease in waste.Streamline production processes: Optimize your production workflow. By identifying bottlenecks, you can improve efficiency and decrease downtime. For example, a manufacturing company could reorganize its assembly line to enhance speed and output.Invest in employee training: Equip your team with the skills to operate new technologies effectively. A well-trained workforce can adapt swiftly to changes, ensuring competitive operations.Utilize data analytics: Leverage data to make informed decisions about production and inventory management. By analyzing trends, you can anticipate demand and adjust operations, reducing excess costs.Collaborate with suppliers: Build strong relationships with suppliers to negotiate better terms and ensure timely delivery of materials, helping maintain a steady production flow and lower costs associated with delays.
These solutions can be implemented immediately with the right resources and commitment. By embracing innovation, you can not only survive but thrive in today’s competitive marketplace.
To implement these strategies, integrate laser technology into your production line. Start with a small-scale initiative to assess its impact on precision and waste reduction. This allows you to observe immediate outcomes and understand how it can enhance operations.
Next, analyze your existing production processes. Identify one bottleneck and focus on optimizing it, which may involve reorganizing your workflow or investing in advanced tools. These adjustments can improve efficiency and reduce downtime.
Invest in training for your team. Schedule a workshop to familiarize them with new technologies and processes. A skilled team is essential for maintaining a competitive edge.
Utilize data analytics to make informed decisions. Monitor key performance indicators related to production and inventory to identify trends and adjust operations accordingly.
Finally, strengthen partnerships with suppliers. Negotiate better terms and ensure timely delivery of materials to maintain a consistent production flow and lower costs associated with delays.
For more information on how laser technology can transform your operations, visit our Laser CO2 page. Embrace innovation today and position your business for success in the competitive woodworking sector.
6.Leverage Data Insights
In today’s competitive environment, many wooden product manufacturers face rising operational costs. Companies in this sector that do not utilize data insights may miss considerable savings. Neglecting this opportunity can lead to waste and inefficiencies.
Have you considered how much time and resources you could save by effectively using data? Without actionable insights, your production processes might stagnate, hindering your ability to compete. Not adapting can result in a loss of market share and decreased profitability.
There are concrete strategies to leverage data insights, which will be discussed in the following sections. Get ready to transform your operations and enhance efficiency.
The challenge of utilizing data insights can lead to missed savings and efficiency opportunities. For example, a woodworking manufacturer discovered their production line was operating at 70 percent efficiency. By analyzing data, they identified bottlenecks and refined processes, increasing output by 20 percent.
Imagine the frustration of seeing competitors optimize operations while you struggle to keep pace. If this continues, you risk increased costs and potential market share loss.
Every day, you face obstacles in meeting production demands while maintaining quality. Without actionable insights, these challenges grow, making it harder to stay competitive in the woodworking industry.
To harness data insights, consider these actionable solutions:
- Implement real-time monitoring: Use sensors and software to track production efficiency. For example, a CNC manufacturer may install IoT devices to monitor machine performance, enabling timely adjustments and reducing downtime.Conduct regular data analysis: Schedule weekly reviews of production data to identify inefficiencies. A manufacturing company might discover that a specific machine consistently underperforms, prompting necessary maintenance.Train staff on data utilization: Equip your team to interpret data. Workshops can empower employees to make data-driven decisions, leading to a proactive approach to problem-solving.Utilize predictive analytics: Invest in software that forecasts production needs, assisting in effective resource planning. Understanding peak production times can optimize staffing and material usage.Collaborate with data experts: Partner with consultants specializing in data analytics to implement best practices tailored to your operations.
By applying these strategies, you can transform operations and enhance efficiency. Each solution addresses rising operational costs while maximizing your competitive edge.
To utilize data insights, start with real-time monitoring. Install sensors on one machine in your production line to track efficiency and make immediate adjustments. You may achieve results more quickly than expected.
Next, review your production data weekly. Identify one inefficiency and brainstorm solutions with your team. This collaborative approach empowers your staff and fosters continuous improvement.
Consider training sessions on data application to equip your team with skills for effective interpretation. This investment can enhance decision-making.
As you implement these strategies, adapt them to your context. If production demands fluctuate, adjust your monitoring and analysis frequency accordingly.
Connect with us for tailored strategies and support. Together, we can enhance your operations and help you remain competitive in the manufacturing sector.